eGuide
Limit the Costs of Bottlenecks
Supply chain bottlenecks can slow inventory, increase costs, and sabotage brand promises, eventually draining your finances. Here’s how to structure your decisions to address common challenges and limit runaway costs.
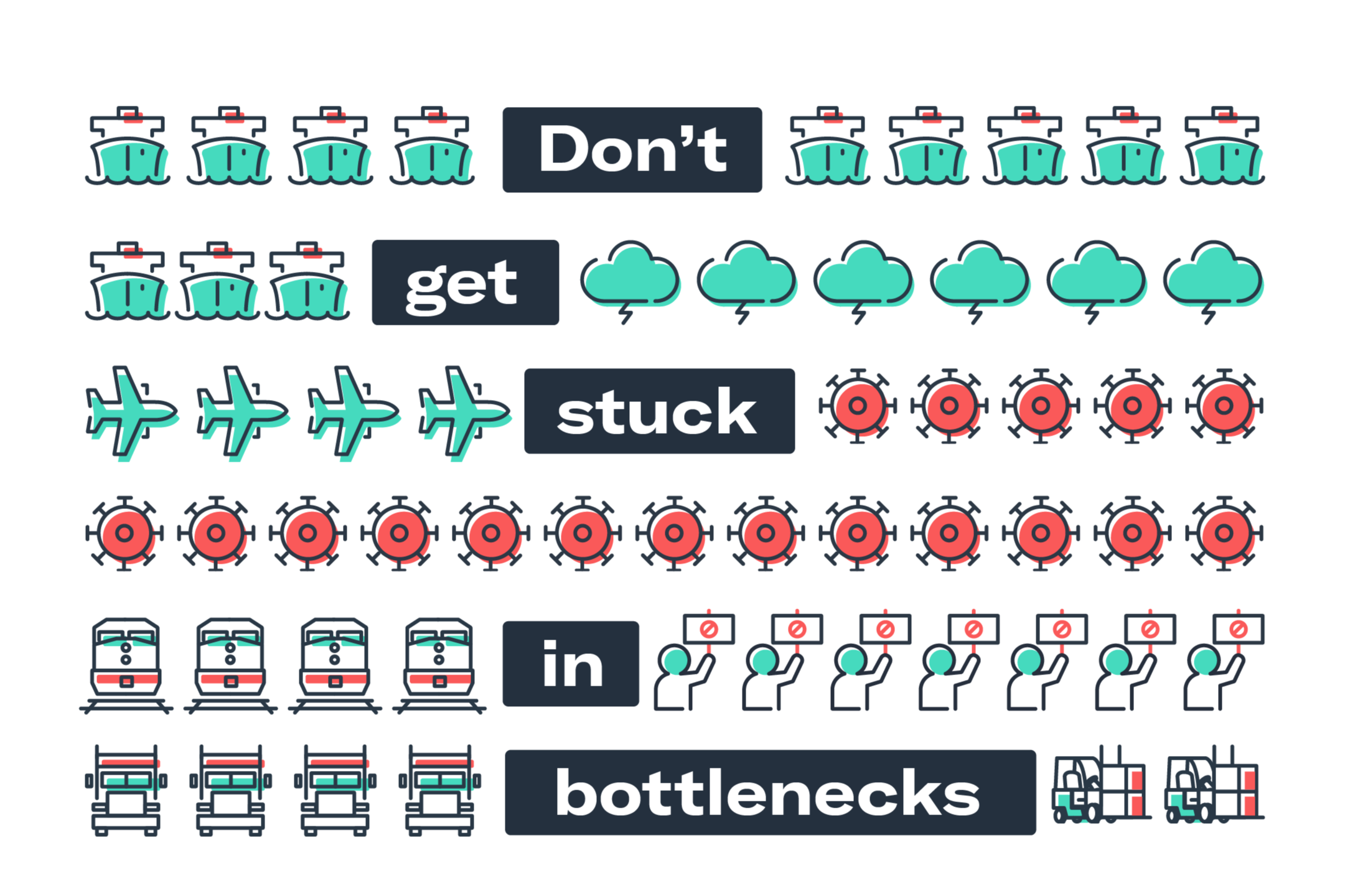
Key Takeaway
Bottlenecks are becoming more complex as supply challenges evolve. Solutions must address root causes.
Key Takeaway
Look at cargo-ready dates and other data to find ways to reduce the cost liabilities of delays.
Key Takeaway
When challenges are global, certain types of restructuring may mitigate ongoing cost leaks.
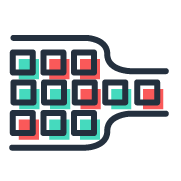
Pinpoint Your Bottlenecks
Identify every chokepoint. Forecasts may miss the mark as suppliers struggle. Congestion impacts multiply as warehouses overflow. Get clear on what you control, what you don’t, and what it costs.
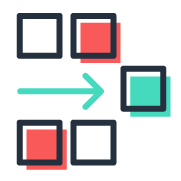
Interrupt Disruption Earlier
Use advanced data and tools to help goods flow. Collaborate with suppliers on orders. Track down to the item. Review shipping routes and partner performance. Not all issues need to be obstacles.
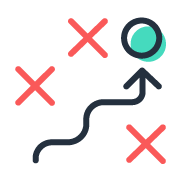
Restructure for Growth
Turn coping mechanisms into competitive advantages. As bottlenecks unclog, you can redirect capital to invest in long-term growth solutions like new logistics hires or nearshoring.
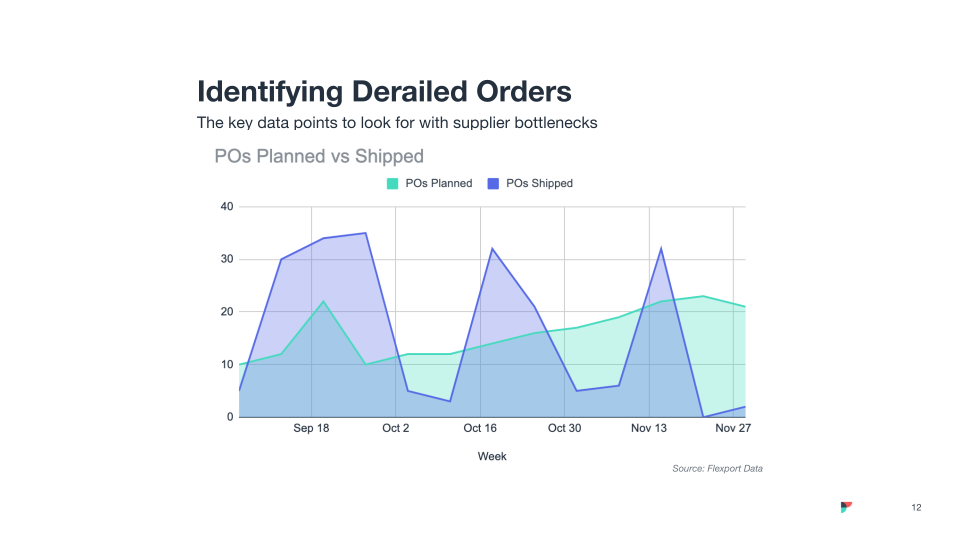
STRATEGY
As Challenges Evolve, So Can Solutions
Many importers feel the sting of the bullwhip effect. That’s when items are available in uneven batches, due to compounding volatility along the supply chain.
Here’s how it happens: When forecasting, companies look to demand trends to drive their raw material or product orders. But demand shock, like what occurs in a global pandemic, can distort the view in a number of ways. As each company along the supply chain makes decisions on fragmented information, availability imbalances grow. These imbalances cause widespread disruption.
Right now, the disruptions include slow or partial fulfillment, missed cargo-ready dates, long transit times, port charges, and congestion. They impact everyone, and the cost impacts spread across supply chains in direct and indirect ways.
Case in point: Transit time from China to Europe can average up to 112 days, up from 50 to 60 days in 2019. This is due to several unpredictable factors, like Covid-related lockdowns and labor shortages, but it’s also because cargo readiness is uneven, driving demand for vessel space higher.
Accordingly, cost follows demand, but cost also follows disruption. This means companies are dealing with two evolving challenges. First is higher rates caused by the global bottlenecks that result from a bullwhip effect. Then, additional costs arise from company-specific bottlenecks that occur when trying to get goods moving again.
In the face of such complex challenges, arm yourself with new insight to create new strategies.
Flexport empowers you to access the data you need, build reports that call out or visualize where inventory is blocked, and compare costs across scenarios. With our supply chain experts offering continuous resources, it’s easier to free yourself from the intricacies of bottlenecks.

Build Resilience to Beat Bottlenecks
Forecast with More Accuracy
Up to 24% of worldwide supply chain disruptions directly impacted Europe in 2021***. Any time one of those disruptions occurred, forecasts for that time period were likely ineffective, requiring your company to act with urgency or lose sales and erode customer trust.
As disruptions become more common, predictive data can help you understand what your inventory may look like, based on transit times. With a model that combines historical shipment data and carrier schedule estimates, you may be able to arrive at more accurate predictions.
This data may be able to help you rapidly adjust forecasts when crises occur, too. That’s because the data model incorporates information like the transit and dwell times from supplier to port, at or between ports, and which ocean carriers and trucking carriers are involved.
Combined with real-time vessel and shipment updates, this can create a more accurate forecast than benchmark lead times that may not apply anymore.
Additionally, as historical data becomes less useful, companies can complement predictive data with humans in the loop to help give qualitative context to numbers.
For instance, average 2021 transit times from China to Europe show sailings from Qingdao increased by approximately 55 days. Shanghai went up by 47, Ningbo went up by 46, and Yantian by 39****.
Should you concentrate on Yantian and avoid Qingdao in 2022? Not necessarily: Yantian experienced terminal closures in Q2 2021 that diverted sailings and increased congestion in other ports. Your data doesn’t always know things like that. Humans do, making a mix of forecasting resources vital in the battle against bottlenecks.
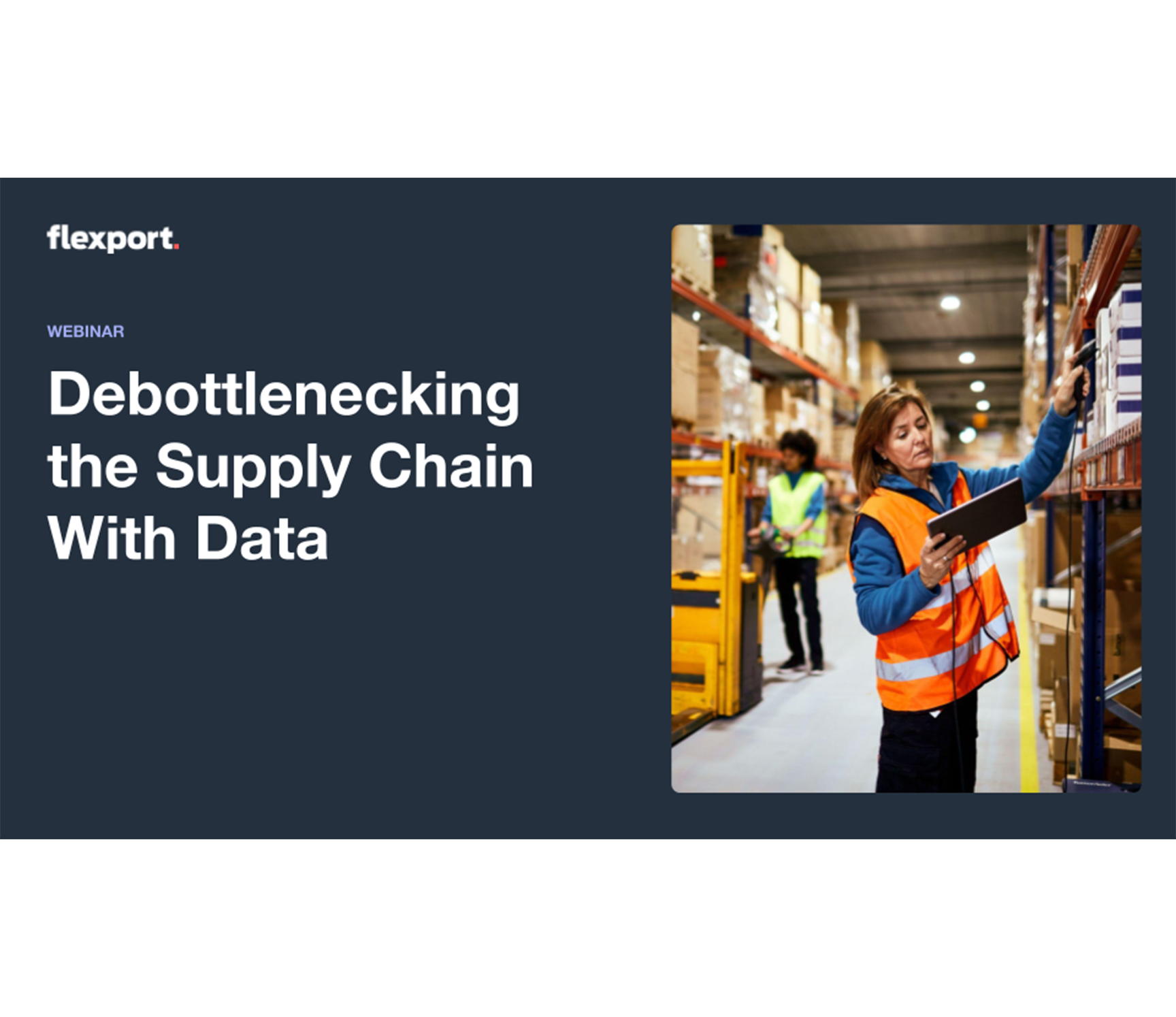
DATA
Use Data to Ease Bottlenecks
Look at how different industries can resolve their pain points with specific data points, metrics, and an understanding of the trends at play today.

Optimize Inventory Strategies
Being able to provide real-time data in the right quantities helps drive successful procurement. When customers and internal teams are up to date, they can make the right decisions for smooth inventory planning, even when supply bottlenecks are imminent.
When global situations move beyond your control, you can make clear lists of priority items. Share them with suppliers, so you get what you need first, instead of managing lower priority inventory at the expense of sales revenue.
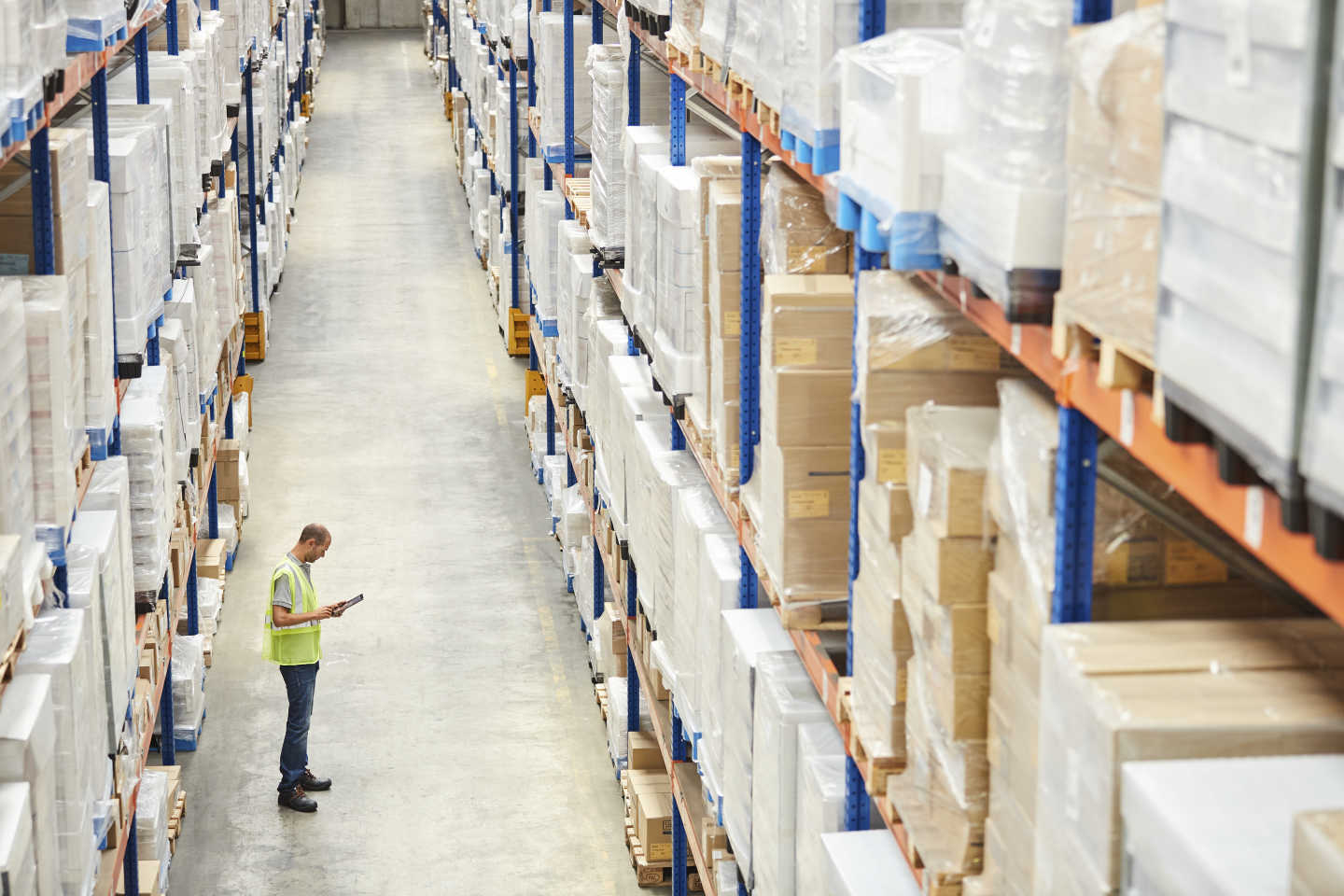
Manage Supplier Performance
Pay attention to your cargo-ready dates. They’re one of your most important indicators. Compare the purchase order CRD to the actual CRD. Then, calculate the cost when you have to rearrange everything downstream.
In some cases, you may need to adjust your supplier mix for greater reliability. In other cases, all suppliers may be impacted by material shortages, Covid-related lockdowns, and jagged demand that pressures their ability to procure or produce.
This is what has happened to bicycle manufacturers over the last two to three years. The category has faced severe supply shortages of key components, as demand for cycling skyrocketed during the pandemic. As a result, factories have increased production lead times, causing brands to experience extreme supplier bottlenecks.
Combat their impact by making sure suppliers keep you updated. That way, you can plan accordingly if delays persist.
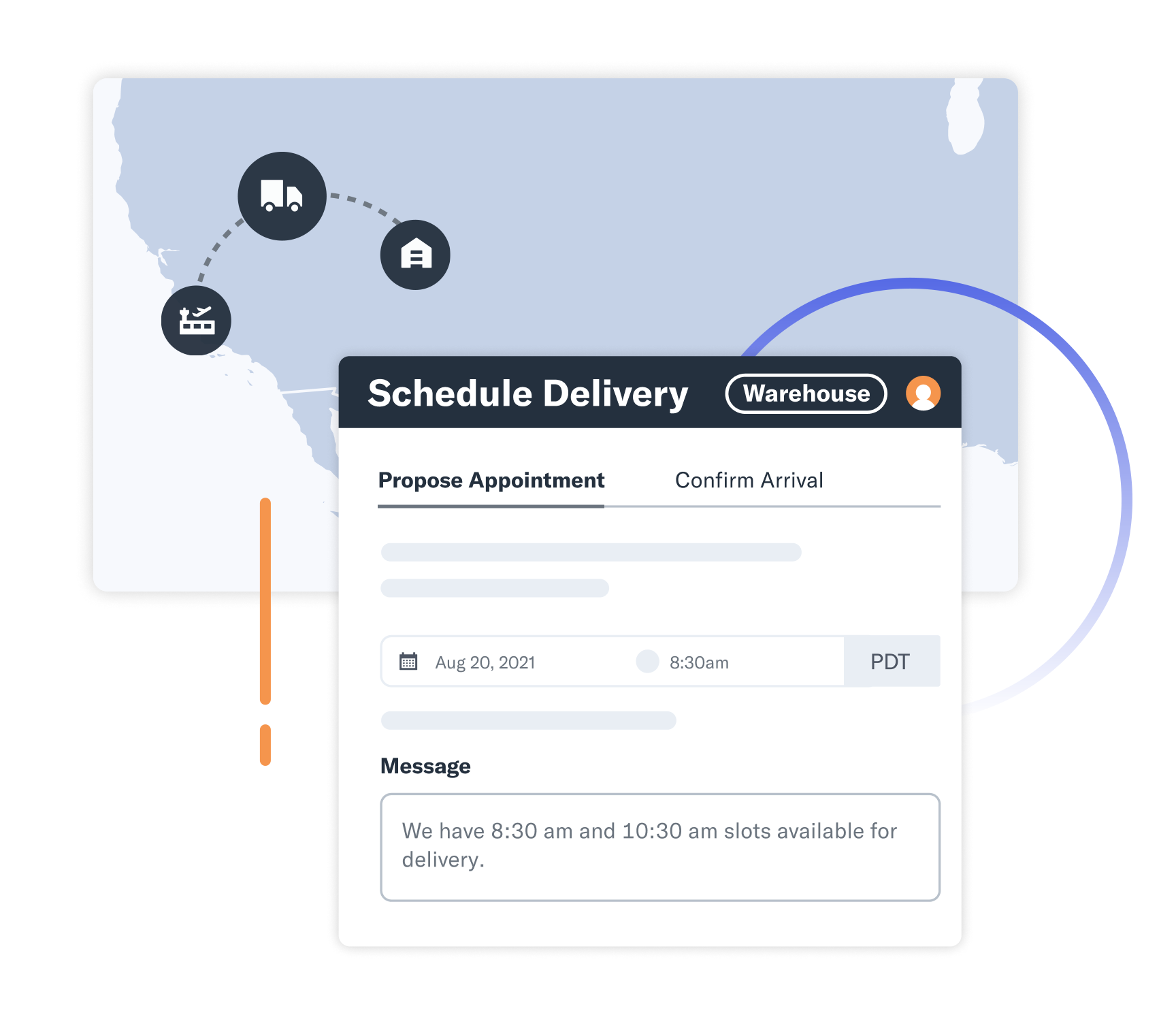
Align with Warehouses
Warehouse space is at a premium in Europe. With little land available and environmental regulations constraining development, it’s likely we won’t see enough new warehouses to help ease congestion in the near future. You have to get better at using the warehouses you have—or pay the price.
There are a few ways bottlenecks cause cost increases at this leg of the journey. The main one is misalignment between truckers and warehouses. Truckers experience their own schedule disruptions, waiting in long lines at borders, ports, and warehouses. They may arrive at warehouses when they can, only to find there’s no available appointment slot for a pickup or drop off. When this happens, they have to leave and return later.
The solution: Work with drivers and warehouses to reduce turns and control cost.
Through Flexport’s Warehouse app or your own Warehouse Management System, teams can communicate some or all of the following data points to optimize delivery planning:
- Last free days before detention and demurrage fees
- Prioritization of containers, based on forecasts
- Whether containers are floor loaded or palletized
- Cargo volume or estimated time to unload
You can further strengthen your supply chain with features like digitized documents that all partners can easily access, real-time notifications when exceptions occur, and centralized messaging across partners. These types of features help you and everyone else stay organized, so that if a truck driver gets stuck somewhere or a warehouse is overflowing, you know and can act to mitigate extra expenses as soon as possible.
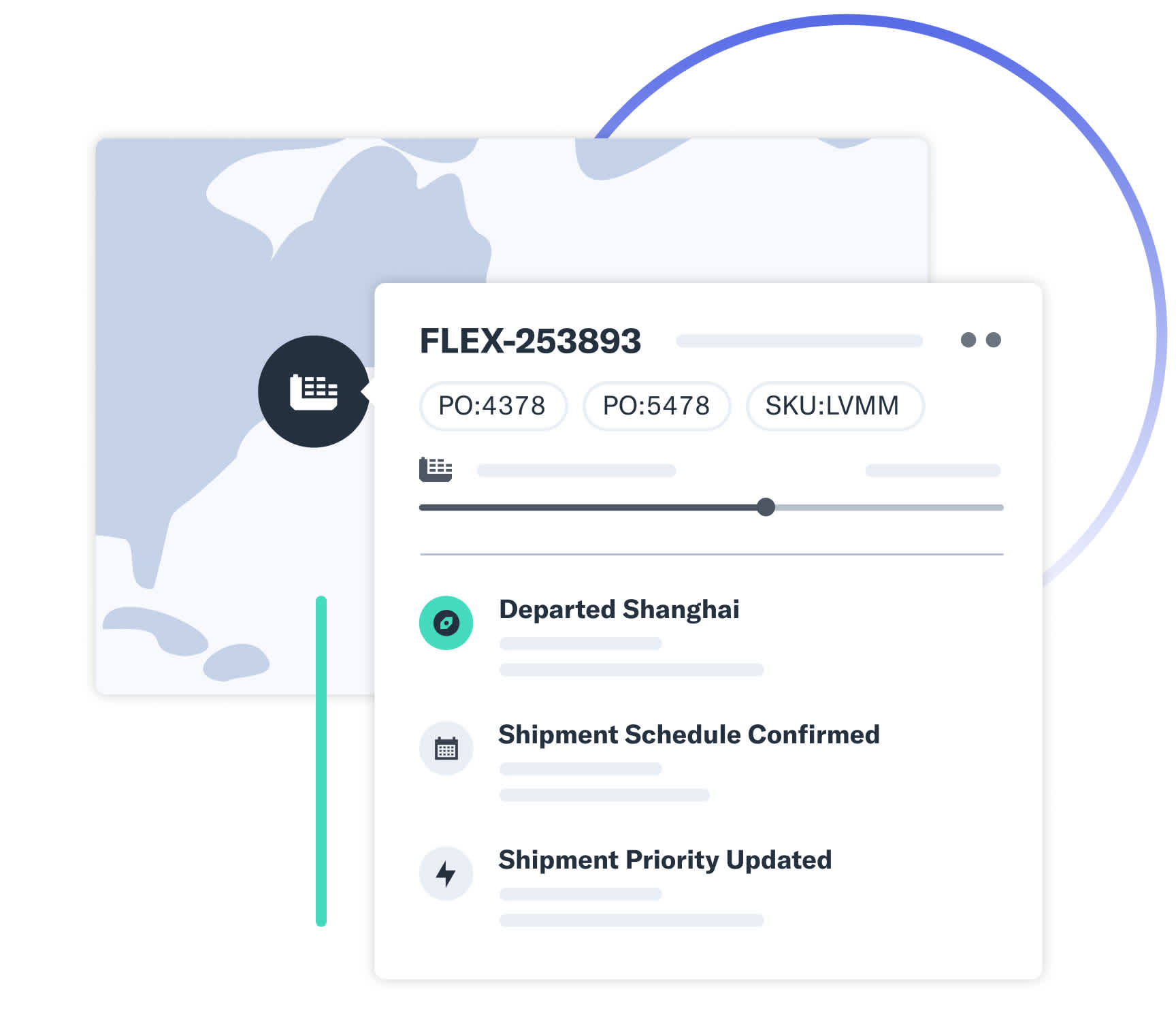
RISK MITIGATION
Catch Bottlenecks Before They Happen
See more on scenarios that could threaten your supply chain. Factors like lack of tracking, unstructured process, and disorganized documentation can lead to wasted time and wasted money. When you know more about how to connect the different parts of your supply chain end-to-end, it’s easier to beat bottlenecks.
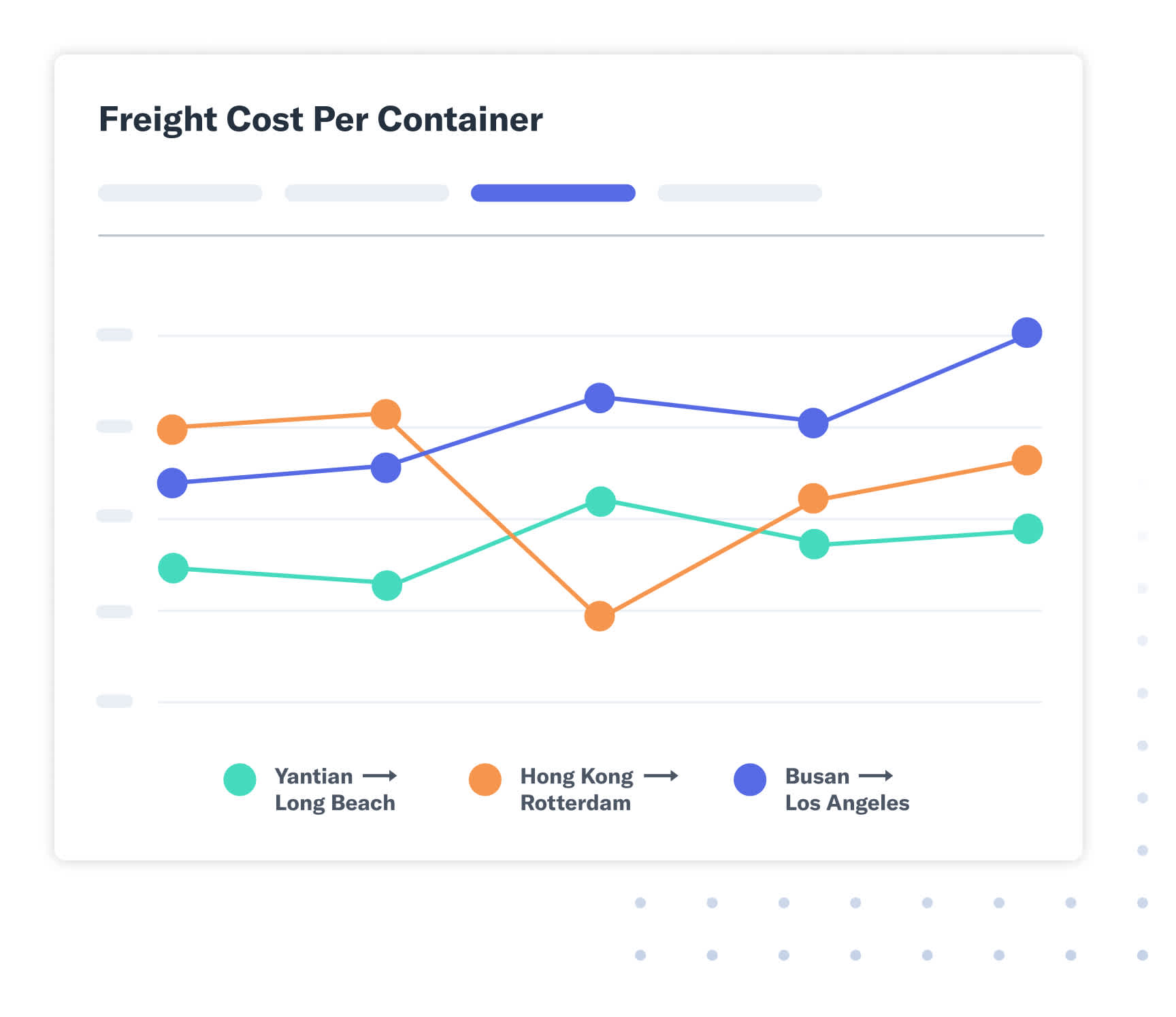
DUAL SHORING
Cost Factors to Streamline Sourcing
As congestion and cost jeopardize supply chains, some companies turn to nearshoring, the act of bringing sourcing closer to distribution. This strategy has its own expenses, like building out factories or paying more for labor, but the positives can outweigh the negatives.
Nearshoring helps diversify your suppliers and restores predictability. Essentially, you may experience fewer bottlenecks when there are fewer legs to your logistics. You can also greatly reduce your carbon footprint.
Consumer price tolerances also mean companies may not pass on all of the costs of bottlenecks. Limit those costs in the long run by splitting your sourcing between Asia and a closer location.
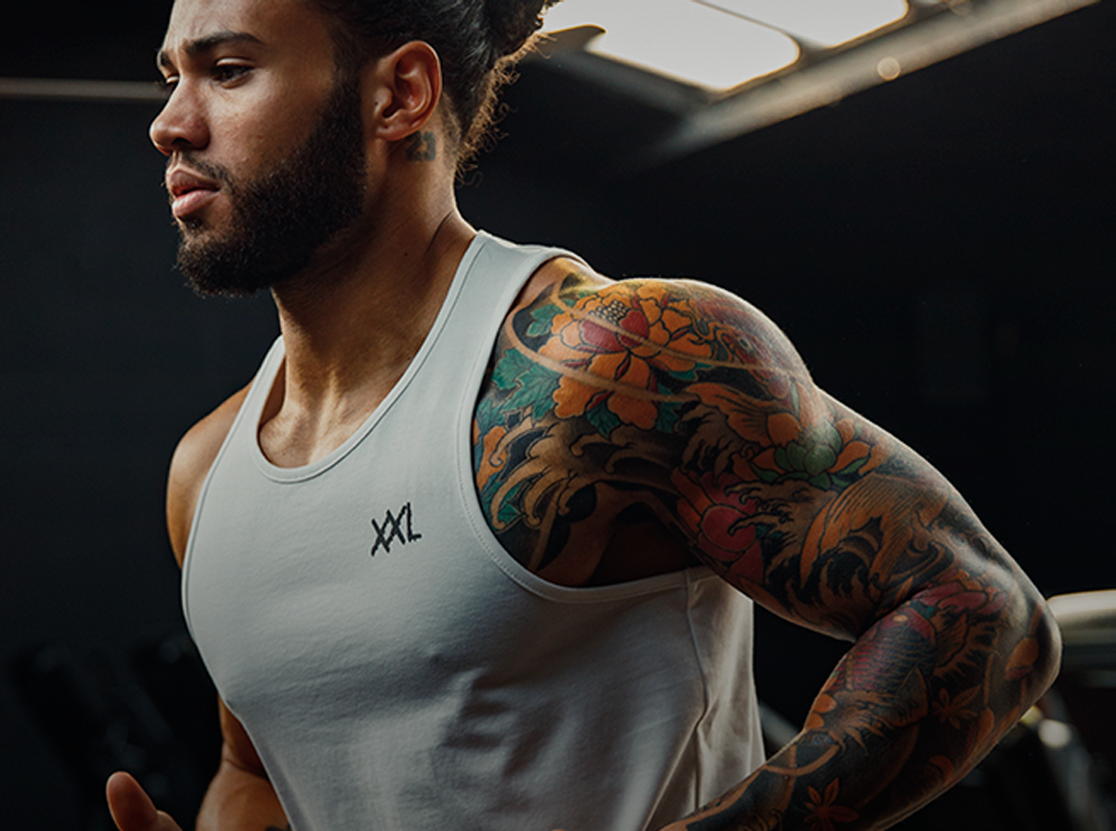
CASE STUDY
A Nutrition Company Supplements Its Suppliers
When Dutch company XXL Nutrition expanded its product array, its supply chain grew in complexity, comprising ingredients from various origins. Digitization and centralized communication in the Flexport Platform allow buyer Roel Linders to manage inventory effectively, replenish stockouts quickly, and increase customer loyalty during a period of rapid growth.
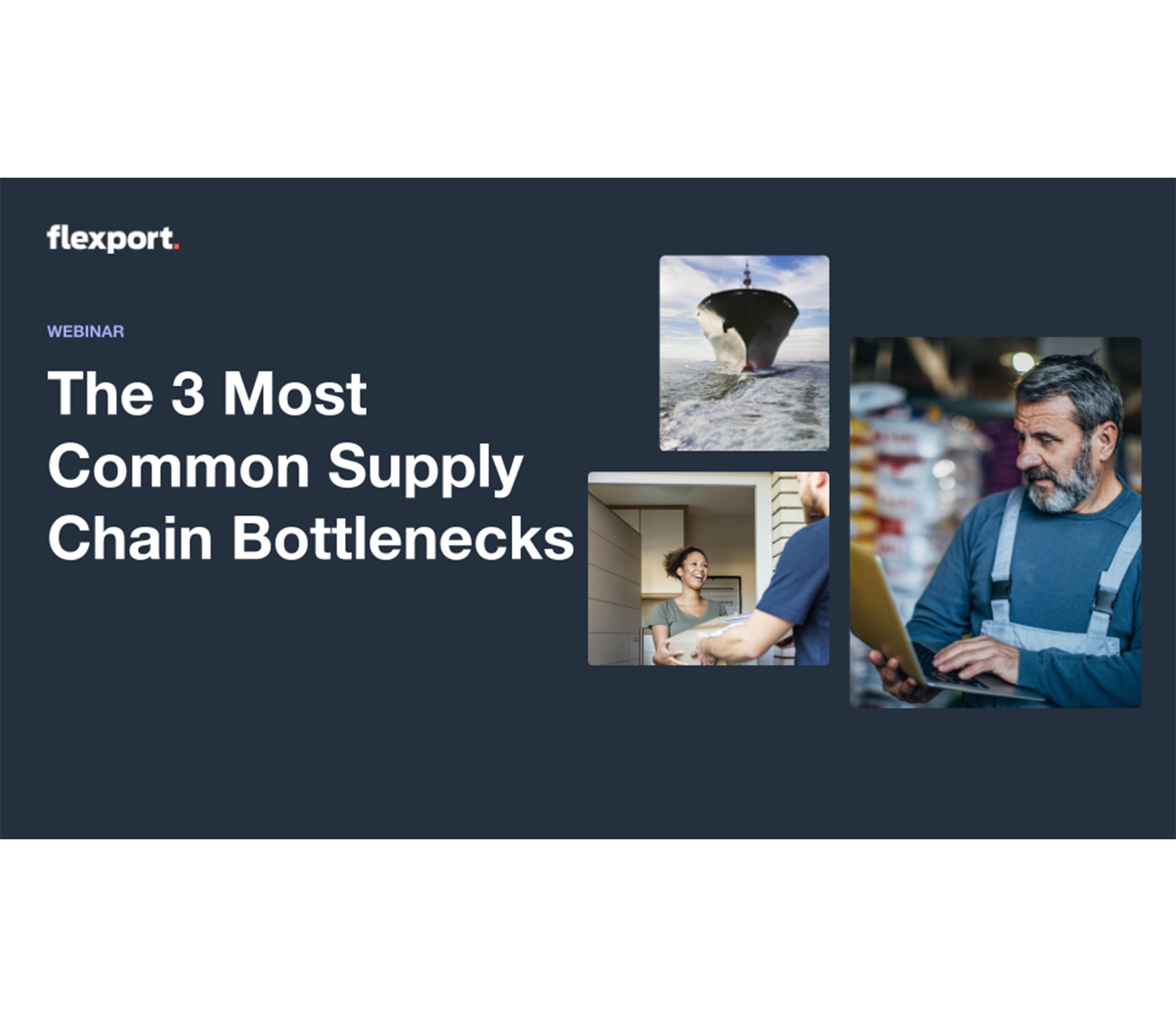
INSIGHT
Overcome 3 Common Bottlenecks
Hear more from Flexport experts on how to solve common bottlenecks and optimize your supply chain for greater predictability in uncertain times.