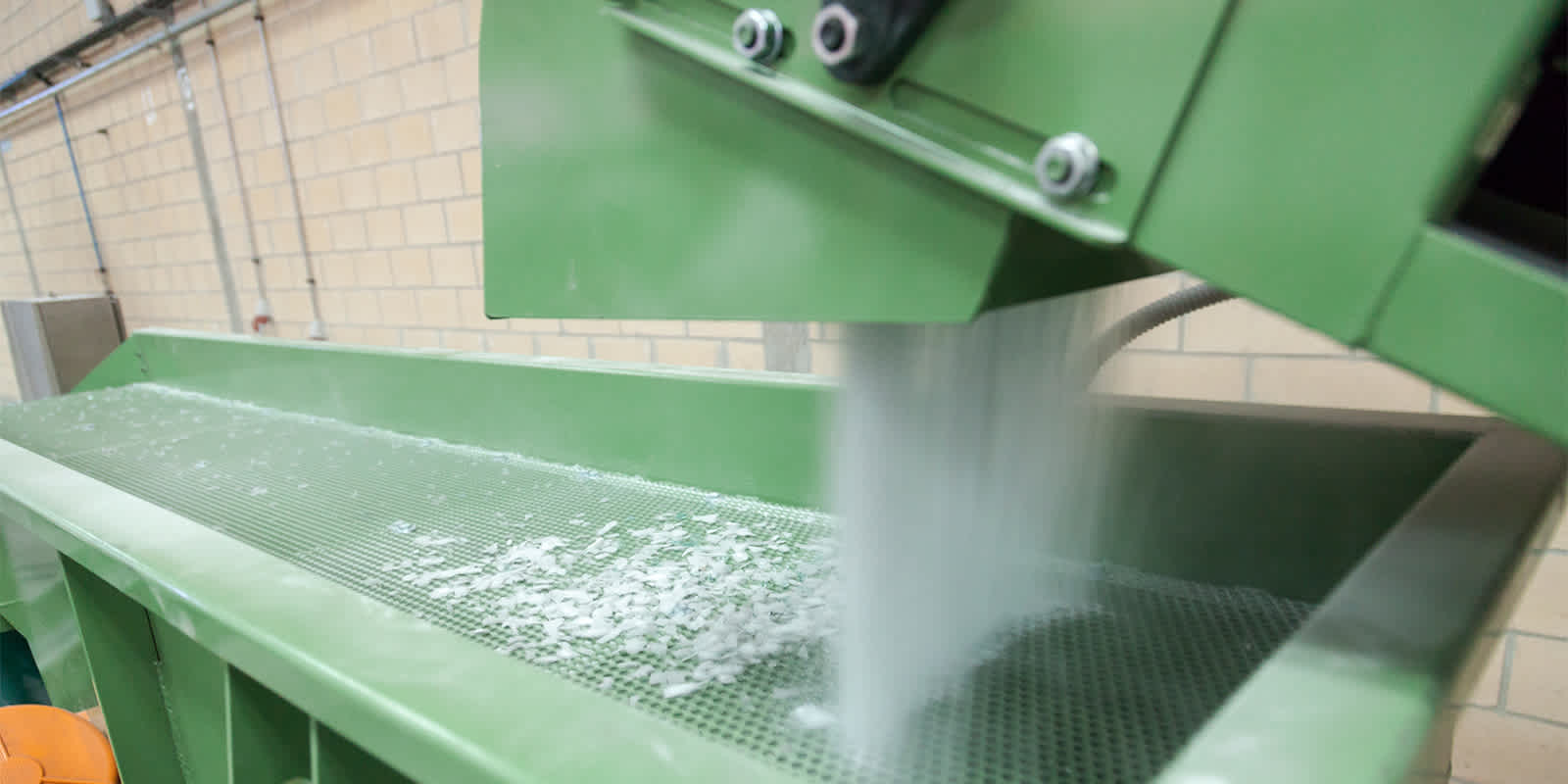
March 15, 2021
Beating the Bullwhip Effect: Can Supply Chain Imbalances Be Fixed?
Beating the Bullwhip Effect: Can Supply Chain Imbalances Be Fixed?
A year after the initial onslaught of Covid, supply chains around the world are still experiencing serious havoc. A bullwhip effect has taken over recovery efforts, as supply variability upends companies attempting to meet shifts in demand.
The result is a global trade environment full of mixed messages: an upswing here or a speed bump there, causing ripples of reactivity that can snarl even short-term forecasts.
To survive, companies need to grab the bullwhip by the handle and straighten out the relationship between their supply and demand patterns as much as possible.
What Is the Bullwhip Effect?
At the heart of the bullwhip effect is dysregulation of what current demand means for future supply.
When forecasting, companies look to demand trends to drive their raw material or product orders. But demand shock, like what occurs in a global pandemic, can distort the view in a number of ways. As each company along the supply chain makes decisions on fragmented information, availability imbalances grow.
Purchase order quantities may miss the mark. Factories, playing their own guessing game, manufacture too much or too little, hoping to capitalize on a rush or avoid a price-reducing supply glut. Buyers react by stockpiling what’s available—known as shortage gaming—or scrambling for alternate goods. The chain reaction muddles the demand picture and can mislead suppliers even more.
Going higher up the supply chain, the distortion compounds, just as the wave pattern of a bullwhip amplifies further from its handle.
Just-in-Time Replenishment
Today, trade flows are experiencing the bullwhip effect on a major scale, mostly due to the severity of Covid disruptions. But economists aren’t stunned by the turmoil.
Global vulnerability to a bullwhip effect has been years in the making. Decades of just-in-time manufacturing have sought to eliminate as much supply chain inefficiency as possible, by tightly matching replenishment to demand.
But a just-in-time philosophy can leave companies empty-handed when suppliers misjudge volatile demand signals. In this case, a broad supplier retreat at the onset of Covid has been followed by roaring merchandise demand while consumers wait for services to reappear.
For instance, the World Trade Organization’s most recent quarterly Goods Trade Barometer shows indices for electronic components at 105.1 and raw materials at 106.9.
Anything above 100 is considered above-trend growth. This is likely due to high demand for shinier tablets, gaming consoles, a slew of voice-activated kitchen appliances, and other high-tech goods.
But it’s just as likely that companies are stockpiling inventory.
High demand for tech-enabled goods has resulted in a shortage of semiconductors, the almighty electronic component that controls the Internet of Things. The WTO suggests the heightened index may be at a peak.
And when the semiconductor supply chain catches up with demand, the index may be closer to 100, the figure for on-trend growth.
Another possible resolution: Once more vaccines are administered, at least a few consumers would probably rather go to a restaurant than stay at home and talk to the microwave, no matter how smart it is. Demand for goods may dip as services rebound, helping to close any lingering supply gaps.
Counteracting the Bullwhip
While companies wait out the uncertainty, rebalancing forecasts remains challenging. Economic stabilization may not occur for months. Instead, supply chain directors and buyers can manage factors internally to mitigate imbalances.
- Optimize inventory. Manage product arrays by limiting inventory to core offers—a best-selling t-shirt, a signature colorway—or opt for smaller orders and shorter product cycles. There’s a silver lining here: SKU proliferation can be a source of inefficiency, even in so-called normal times. Use this chance to prune wisely.
Reducing inventory complexity may make it easier to keep goods flowing. For better visibility, use Flexport’s Order Management system to manage purchase orders against larger business cycles.
- Strengthen supplier relationships. Hyper-efficiency might not happen for a while. But there is a real opportunity to get in good with crucial suppliers. In the Flexport platform, even casual communication takes place in context, attached to orders or shipments.
Ask about continuity for products and raw materials, especially in industries experiencing shortages. A “Thank you and could you let me know if . . .” message under a shipment could save the day up ahead.
Fortify your supply chain further by looking for alternate suppliers and figuring out related shipping routes, in case new shortages strike. Just don’t double down on cracking the bullwhip unwittingly. Be clear about possible future orders or provide range forecasting to avoid misunderstandings that could push supply flows even more off-kilter.
- Empower velocity. Prepare procurement and logistics teams to get through business challenges quickly with end-to-end information in real time.
Live, personalized insights into priority shipments, exceptions, and maps mean logistics managers can jump right into problem solving—or, even better, see problems coming—before business gets off track. When it comes to planning, a customizable reporting center helps reduce risk and close the gaps that create the bullwhip effect in the first place.
For additional tools to help regain control of inventory during worldwide supply and demand imbalances, get started with Flexport Order Management.