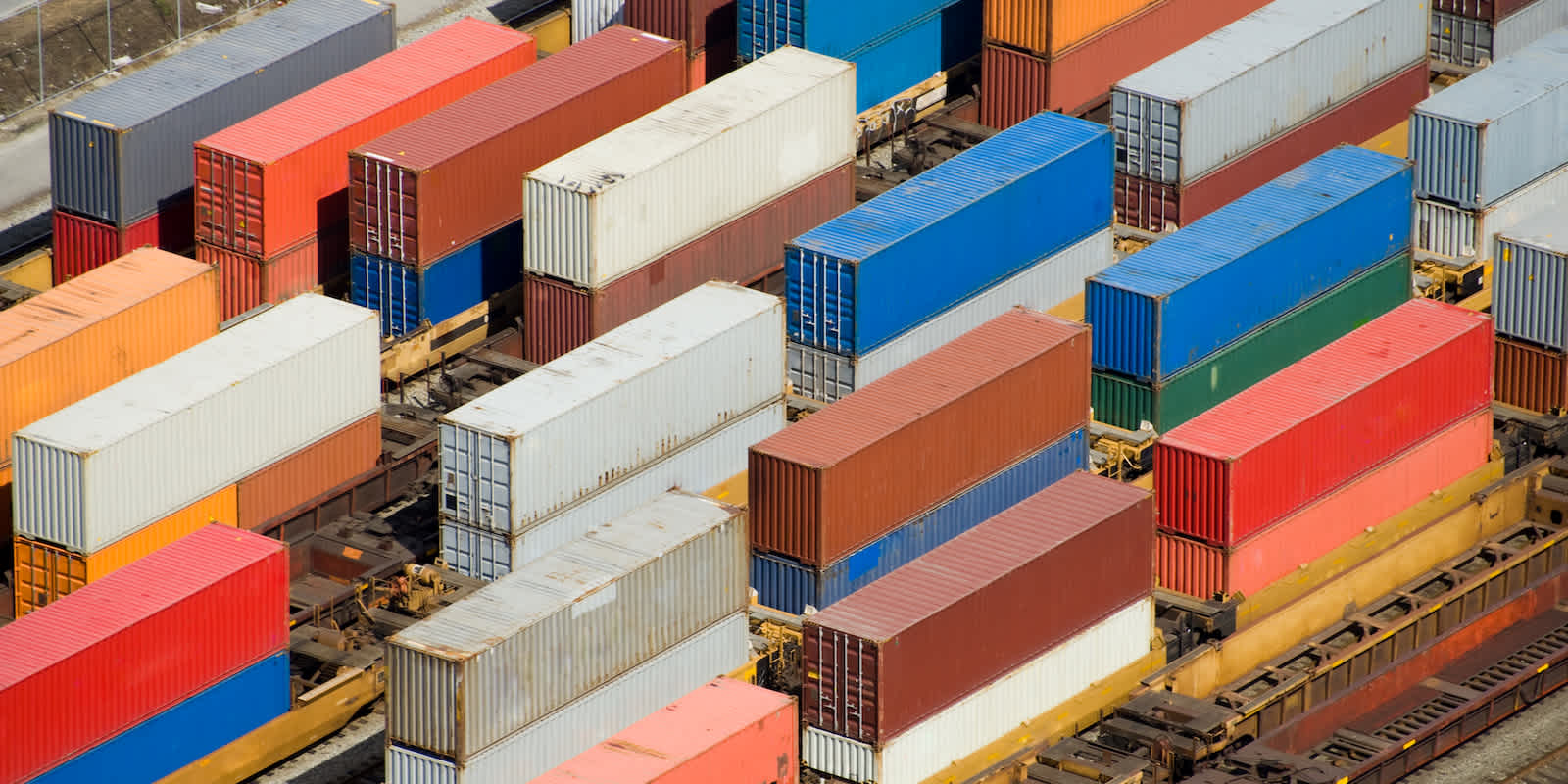
November 9, 2022
Addressing the Root Causes of Supply Chain Bottlenecks
Do any of these logistics scenarios sound familiar to you?
- “Where did these demurrage and detention charges come from? My team doesn’t have the budget for this.”
- “Last week a container showed up without warning and there was nobody at the warehouse to unload it. All I’ve got to work with is an ETA for when the cargo will arrive at port. I know nothing about when it will arrive at our warehouse.”
- “My goods are stuck in Customs control and now I face heavy contractual penalties because we couldn’t hold up on the agreed deadlines.”
- “Communication with my suppliers is spotty at best. I leave voicemails, then wait to get a status update. Meanwhile, I’m busy putting out the fires that start because I can’t tell people what’s going on.”
- “Sales, marketing, customer service, everybody comes to me for milestones, and I just don’t have them. Delivery times are so variable these days, and we’re losing customers because we can’t tell them where their goods are or when they’ll get them.”
- “Paperwork is a constant headache for us. Every week, I lose a full day chasing paper trails, sending emails, putting out fires, etc.”
- “I learn about exceptions too late, and if I knew about this earlier, I could have found an alternative solution.”
Each of the above scenarios describes a logistics bottleneck that many shippers are familiar with. Whenever you find yourself waiting on key information in order to keep an order moving—that’s a bottleneck.
Whenever you’re surprised to find a truck at your loading dock that you were expecting next week—that’s a bottleneck.
When a seemingly simple situation leads to orders being delayed, shipments being unaccounted for, or staff looking for missing information—you’re dealing with a supply chain bottleneck.
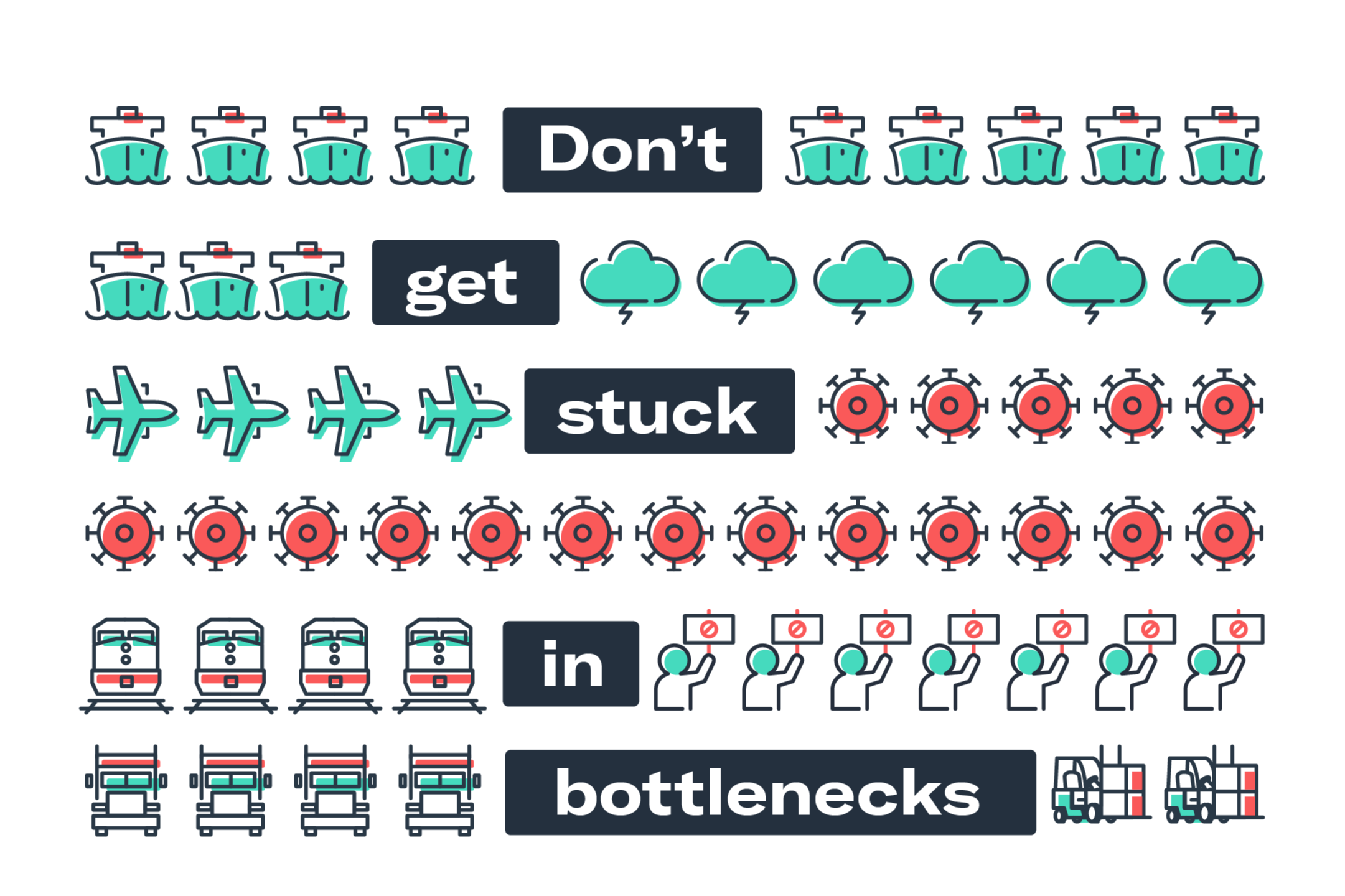
Uncertainty, disruptions, pandemics, and no centralized place to access supply chain information have resulted in many logistics teams feeling like they just don’t have the control or visibility they need. In a discipline that still relies on spreadsheets, emails, and phone calls, gathering the siloed data you need to overcome these hurdles can quickly overwhelm even the most experienced logistics pros.
Identify Your Supply Chain Bottlenecks
To build resilience, it is necessary to look at your end-to-end supply chain and identify the potential bottlenecks that could keep you from achieving the desired results. Solving an issue in one part of the supply chain might be completely pointless if it is offset by a new roadblock somewhere else. In many cases, these bottlenecks come from:
- Areas/processes you do not expect
- Areas/processes that aren’t your priority
- Areas/processes where you have little/no visibility or insights
As the market situation changes constantly, the challenge is to gain visibility into your complete supply chain to proactively correct minor issues before they become major ones.
Four Root Causes of Logistics Bottlenecks
Despite the seemingly diverse scenarios highlighted above, the majority of supply chain bottlenecks can be tied to one of four interconnected root causes: lack of visibility, lack of internal processes, lack of communication, and lack of data.
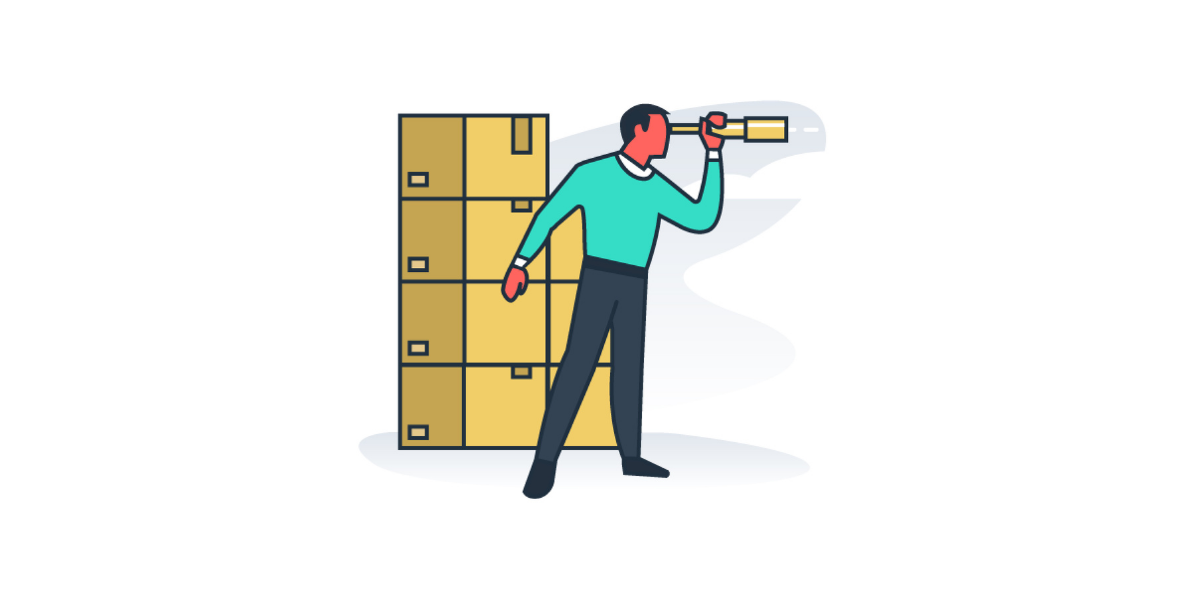
Lack of End-to-End Supply Chain Visibility
The data silos created by each stakeholder in a supply chain using their own spreadsheets and emails to communicate mean that there’s no way to get the overall picture of an order’s status. Suppliers might not send word of a shipment being ready until after it has left the factory, or you may be told the vessel is set to depart today but don’t get notified that it was actually held up three days.
"Flexport allows us to manage how we scale. They helped us manage our supply chain more easily, by providing visibility and allowing us to hold our suppliers far more accountable. Since our supplier works within the system, they have a hand in our success beyond just the production of our product."
- Hector Omoigui, Senior Operations Manager, Reel Paper
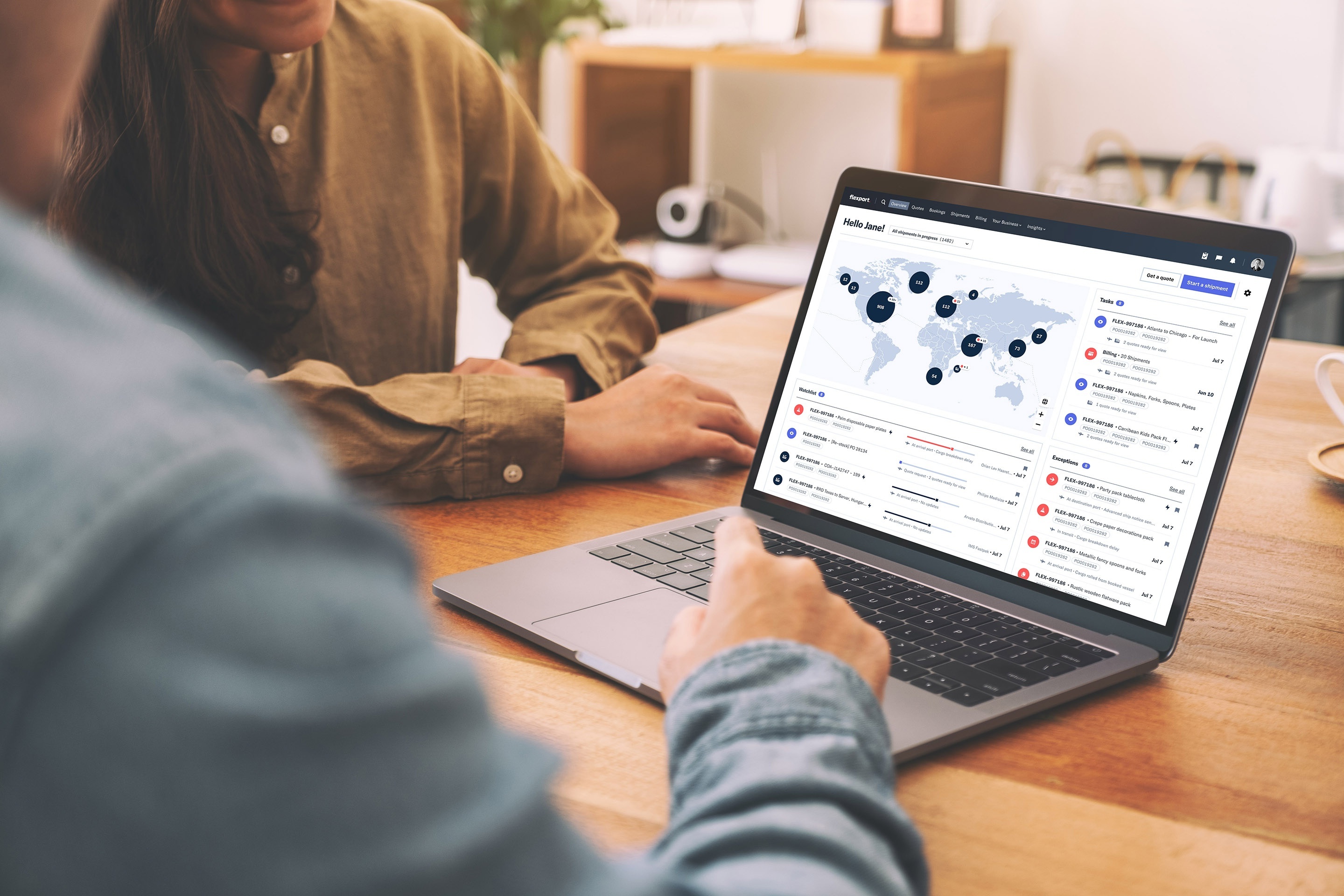
Lack of Internal Processes
Internal processes are easy to run when everything works as it should, but as soon as things get complex, you need to be able to make quick decisions that influence your routing and pricing decisions. Having well-documented and detailed processes helps you avoid these pitfalls and provides accountability in the event something goes wrong.
"Flexport has spent a lot of time understanding our current processes and helped us design better processes for the future. Their platform allows us to stay completely up-to-speed on the status of our orders. Flexport has brought a different view of how to solve our international shipments and revolutionized the way we automate our communications."
- Carter Nolan, Supply Chain Director, Georgia Pacific
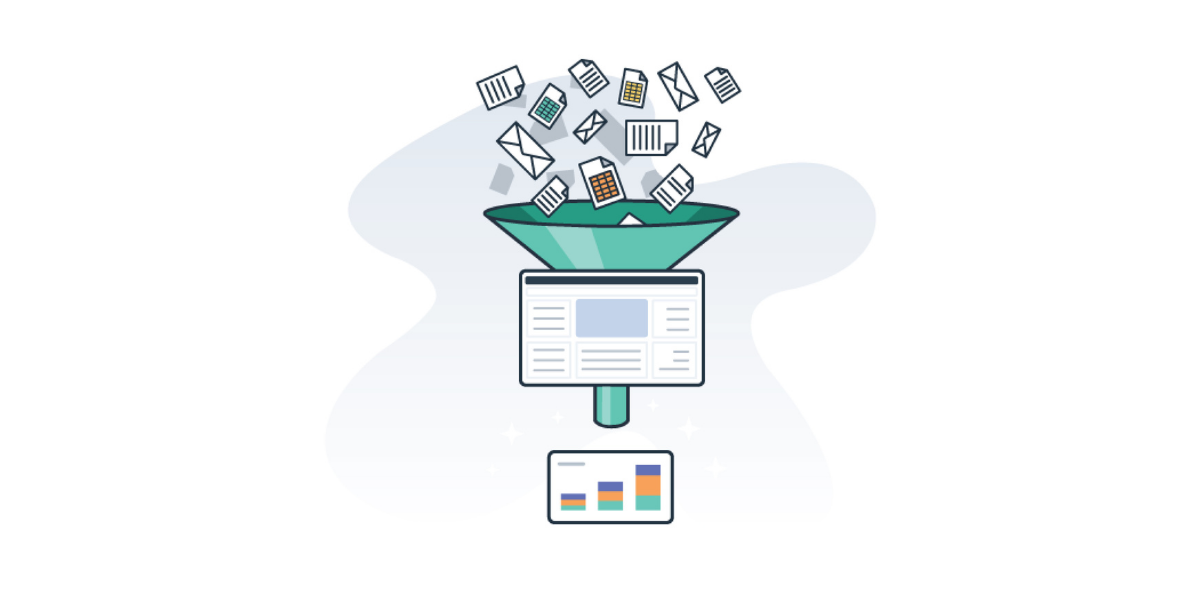
Lack of Centralized Communication and Documentation
Flexport's internal data shows that as many as 25% of customer shipments are impacted by late or missing paperwork. Late or incorrect submission of documents such as the Commercial Invoice, Packing List, and the House Bill of Lading will block or delay Customs clearance, and as a result, delay the final delivery to your warehouse or retail location. By tracking communication and documentation end-to-end, from supplier to customer, all in one place, you’re better positioned to work together to find ways to improve these processes.
“With the Flexport Platform, all the information is at my fingertips. I love the ability to correspond at any time of day and get an answer from somebody. Particularly during the pandemic, I got information from Flexport in China and turned it around to our team in Europe. It sped up our response time and made us more nimble.”
- Ali Ferber Peters, Co-Founder, She's Birdie
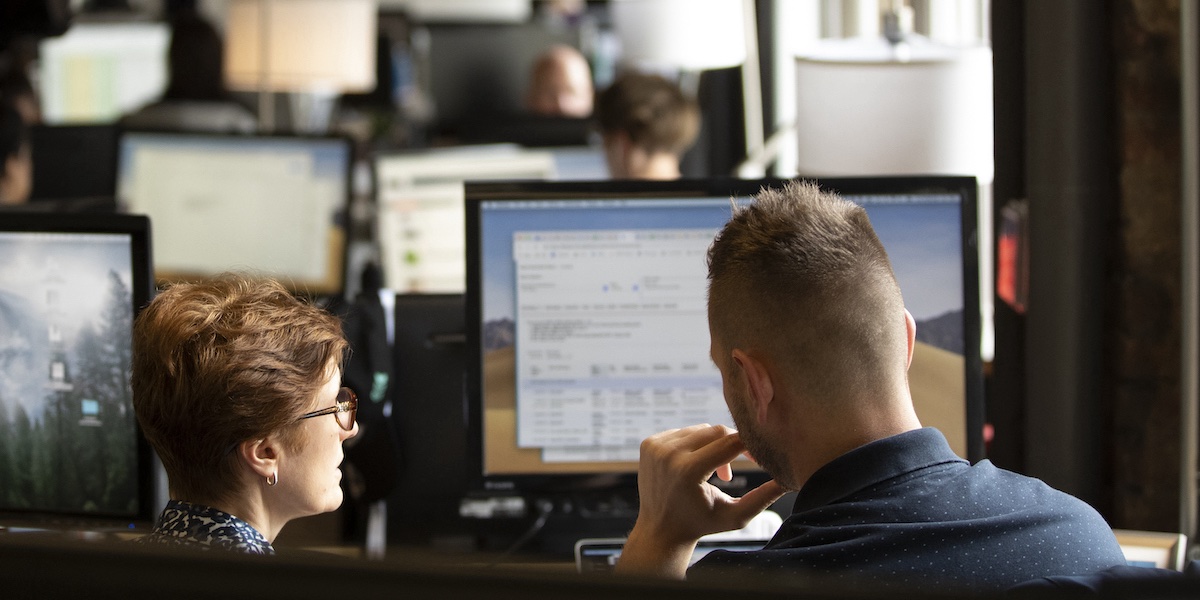
Lack of Shipment Data
Underlying the above three points is a general lack of data about each link in your supply chain. Data powers accurate forecasts, enables real-time updates to customers, and allows for fast decision-making on rerouting and mode adjustments.
“Being able to know what is actually going to arrive at each of our distribution centers at any given time, plan around it, and pivot, as needed, has allowed us to make sure that the right product is at the right place, at the right time, so we can fill large orders. For the customer, it’s seamless.”
- RoxAnne Thomas, U.S. Transportation Manager, GERBER
Not Mitigating These Root Causes Will Cost Your Business
As with any business decision, there are costs associated with leaving the cause unaddressed. For example, a European retailer was paying €600,000 a year in fines and penalties because they couldn't see where their stock and containers were.
Upstream visibility into inventory-in-motion can be a significant value driver as well. BCG research showed that a 15%-30% reduction of working capital could be achieved through better visibility of end-to-end inventory in the supply chain.
Other ways that unaddressed bottlenecks can hurt your business:
- Inaccurate forecasts can lead to stockouts and disappointed buyers who may leave you for a competitor.
- Disorganized internal processes can lead to inefficient decision-making and additional delays in rerouting, price adjustments, etc.
- Missed paperwork deadlines due to an unseen emails can lead to shipments sitting in port, idling warehouses, and accruing excess costs.
- Uneven access to data can lead to team confusion as people are working off of different/old information.
- Not knowing what is in each container, let alone when it will arrive, increases chances of a stockout.
It is possible that addressing one cause can lead to other causes being mitigated and further bottlenecks being cleared. In this scenario, full end-to-end data visibility enables each of the other root causes to be mitigated in turn.
By taking a holistic approach to your supply chain, you’ll be well positioned to make data-driven decisions based on accurate, real-time data.
Addressing The Root Causes of Supply Chain Bottlenecks
As with most business decisions, there are short- and long-term options that will address the root causes of your logistics bottlenecks. Some will be quick and easy to implement, while others may take longer and be more resource-intensive, but all are worthy of your consideration in order to protect your business’ bottom line.
Research shows that companies that integrate digital technologies into their supply chain can quickly improve service levels while cutting costs up to 30%.
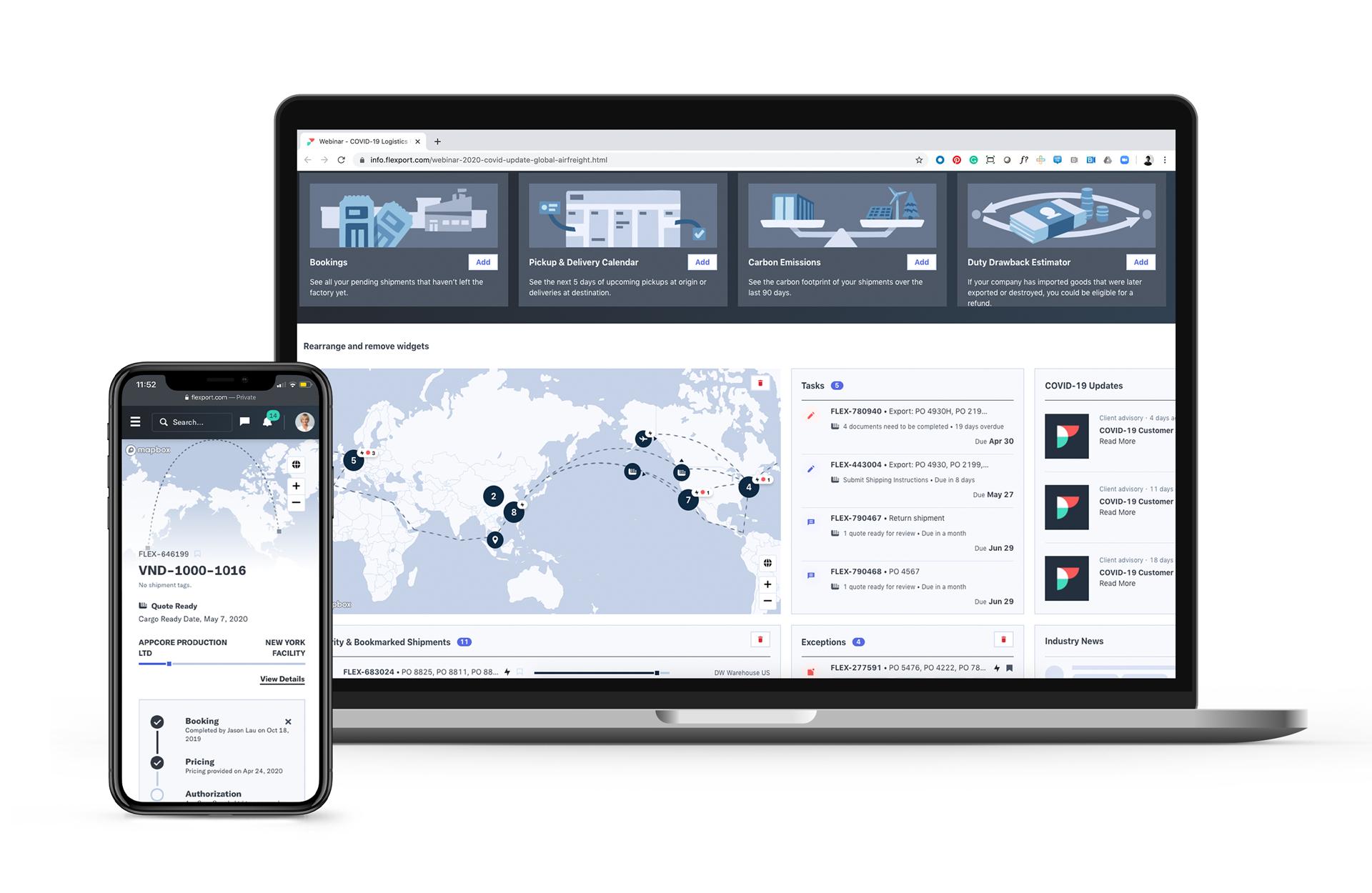
Enable Your Teams To Make Internal Decisions, Faster
You need to first provide your teams with accurate, real-time information on routing, timelines and pricing. Having analytics in place on your complete supply chain setup enables you to make decisions based on real-time data like the latest rates, departure dates, and estimated arrivals—all of which will help you make rerouting decisions as needed. Giving the right people access to the right information at the right time keeps your internal processes running smoothly and your customers in the know.
If your internal processes need a revamp, focus on what you need first. Then make sure that you have a clear escalation process in place, and always give your teams clear guidance about pricing decisions.
Assess Your Internal Data Structure
Start by equipping yourself with the right set of data that will allow you to respond fast to potential roadblocks. Inventory levels, supplier availability, sales volumes, and warehouse space–all of these are important to get a complete picture of the state of your supply chain. Having this data available down to a Purchase Order and SKU level will help you to make the right prioritization decisions. Rapid response will prevent a lot of hiccups from becoming real bottlenecks.
Centralize Communication Across All Stakeholders and Teams
This ensures that your warehouse staff can find out about supply delays and make proactive decisions AND your sales and marketing team knows what is and isn’t available to sell to your customers. This also informs your finance and forecasting teams to help them plan ahead. Your suppliers will get automated push notifications to assure timely upload of documentation, and you'll be able to track all data around delays caused by documentation issues.
Impact on Scenario Planning and Forecasting
Complete historical data lets you make a time series analysis by adding the expected trend (projected sales volumes) and seasonal component to it. We recommend aggregating the forecast by SKU, time, and location, as this will help to reduce variation and will improve the forecast.
Another solution is to forecast with a shorter time horizon and to revise it more periodically. Additionally, we recommend assessing the quality of your forecast by checking the accuracy (how close the forecast is to the actual observation) and bias (what is the persistent tendency to over or under-predict).
Mitigating bottlenecks requires you to spend time, attention, and energy trying to resolve them. Timely identification and proactively addressing bottlenecks will improve your organization's bottom line.
Find out what your supply chain can really do. Flexport can help you identify the bottlenecks you might have missed and provide the expert input you need to address the root causes. Connect with our team of experts for more information.